- Segments
- Process Industry
- Sugar and Ethanol
Maximizing Uptime for Sugar and Ethanol Plants
With decades of expertise, Altus delivers cutting-edge technology and integrated solutions to enhance the control of different systems
For over 40 years, we’ve been creating products and systems to boost industrial efficiency. Our high-availability solutions seamlessly integrate the various processes within sugar and ethanol production plants.
Ask for a advisory
Do you want to implement your current project with us? We will be happy to advise you!
Projects and solutions for the sector
Our solutions for this industry
Distributed control for complete production integration
The high embedded technology in the NX series of modular PLCs allows you to create high-performance control solutions, with resources that can distributedly control all the different processes found in a sugar and ethanol plant.
With a wide selection of analog and digital I/O modules, you can develop architectures that precisely control machinery and equipment for processes such as milling, sulfitation, heating, clarification, evaporation, cooking, centrifugation, drying, fermentation, and distillation.
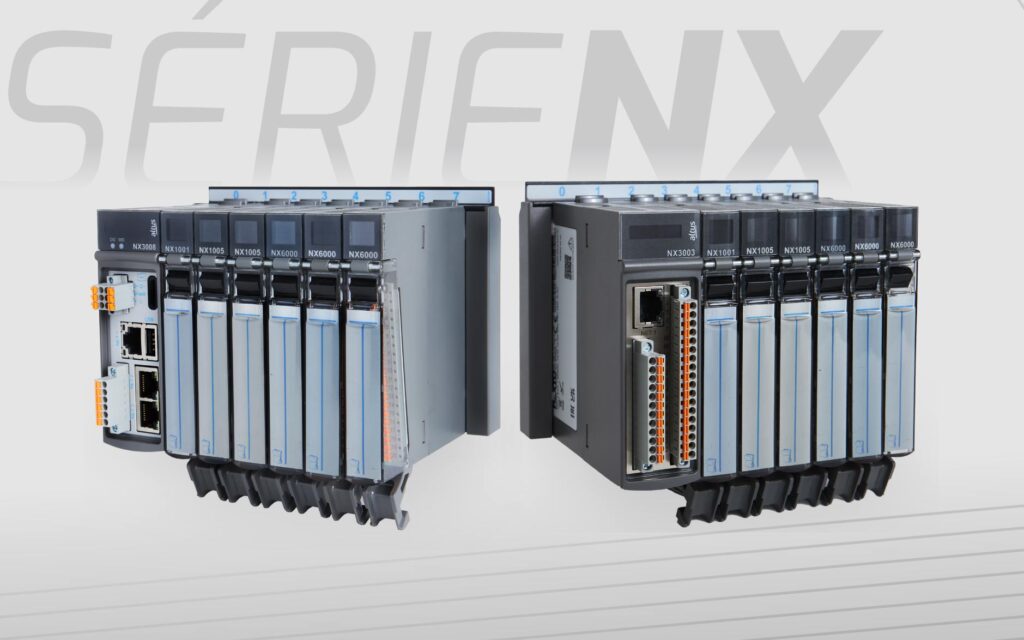
Precision control for sugarcane extraction and processing
In the milling process, Altus PLCs control roller speed and motor load to optimize juice extraction and adjust the cane feed, preventing overload.
In the clarification process, they ensure accurate dosing of sulfite based on the quality of the cane and process conditions, while also maintaining ideal pH levels for maximum juice clarification.
In cooking and distillation, the PLCs regulate pressure and temperature at every stage, control heat distribution, and manage the centrifuges to optimize sugar separation from molasses—keeping the system running smoothly and efficiently without overload.
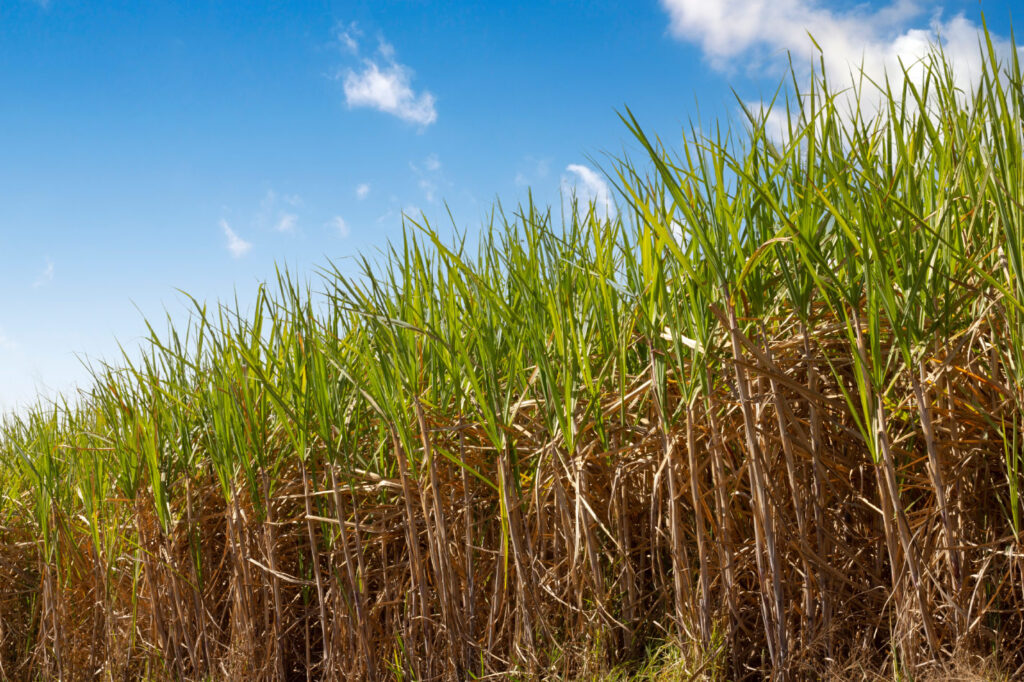
Redundant CPU architecture for uninterrupted operations
The Nexto family of programmable controllers includes a high-performance model that supports hot standby redundancy, ensuring the highest levels of system availability. You can configure a redundant setup with two NX3030 CPUs—one primary (active) CPU running the system, and a standby CPU constantly monitoring its performance.
If the primary CPU encounters an issue, the standby unit automatically takes over, keeping the process running without operator intervention and without disrupting plant operations. This seamless switch-over ensures minimal downtime.
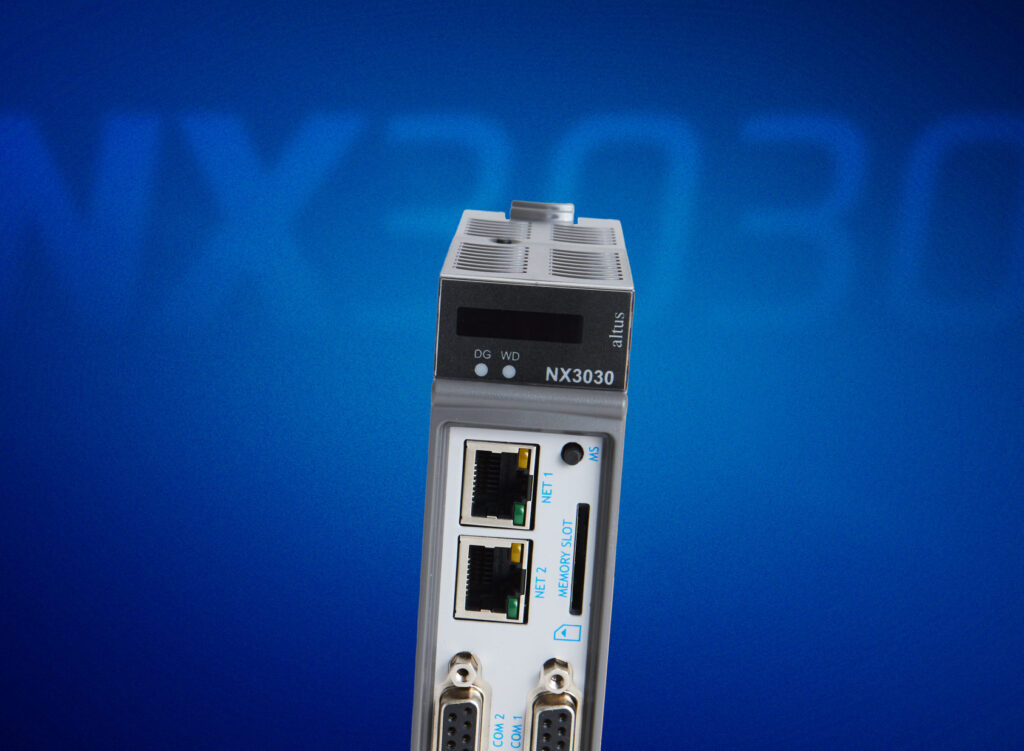
Enhanced protection with conformal coating for harsh environments
All Nexto controllers are treated with a conformal coating process, adding an extra layer of protection to circuit boards, connectors, and critical components against environmental hazards.
This protective coating shields the electronics from moisture, corrosive vapors, and other harmful conditions commonly found in sanitation environments. It effectively extends the lifespan of your equipment by preventing corrosion and ensuring that your automation systems remain reliable over the long term.
This investment in durability keeps your operations running smoothly while safeguarding your technology for years to come.
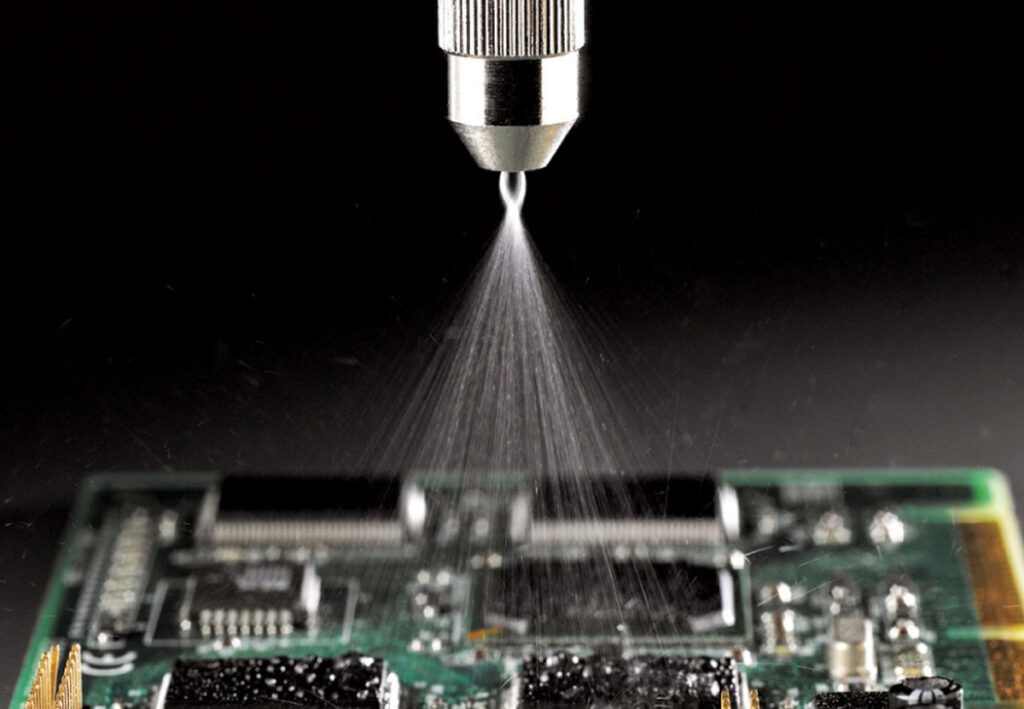